Precision Dispensing System for Membranes - Whey Processor

The Precision Dispensing System for Membranes helped a whey processing plant in the Pacific Northwest improve worker safety, save time, increase productivity, and improve the integrity of their membranes all while saving on cost.
Background
In order to dispense the chemistry, the operator was pumping chemicals into a drum from the first floor to the second, manually pumping chemistry from a drum to a pail and then climbing up a ladder and manually pouring the chemistry into the balance tank.
This process of manually dispensing chemistry led to issues such as:
- Production disruptions from pumping incompatible products from primary containers into day tank containers.
- Safety concerns from operators getting sprayed in the face with chemical due to splashing when adjusting pH during a wash step.
- Reduction in asset integrity from operators adding the full volume of chemistry needed into the balance tank, creating “Tiger Strips” in the solution, where chemistry is mixed by circulation. This creates an un-balanced system.
- Time constraints, as the operator would have to wait longer before completing required pH solution checks.
_
Situation
The plant was looking for a safer and more efficient way to dispense CIP chemistry to their membrane systems and turned to Ecolab for help.
The automated dispensing saved 45 minutes per day compared to previous manual dispensing processes, resulting in an additional 1 hour of production.

Solution
The Precision Dispensing System for Membranes is a safe and accurate, integrated chemical dispenser that helps deliver consistent cleaning results and increased worker safety by:
- Reducing improper chemical handling.
- Eliminating incorrect dispense.
- Minimizing noncompatible chemical interactions.
The Precision Dispensing System for membranes also helps to potentially improve membrane life, by ensuring cleaning solution pH ranges do not exceed manufactures recommendations, and decreases CIP time, by reaching target CIP parameters sooner.
The flow-based system offers separate modules for the acid, alkaline, surfactant and chlorine chemistries and has separate delivery paths for each membrane. It works off of volume-based dosing within 20 milliliters of targeted usage rates, and can dispense up to 5 membrane systems simultaneously.
Additional features include the ability to configure recipes by volume and sequencing to each identified system, as well as out-of-spec alarms, consumption reports and optional PLC integration.
Results
The whey processor was so happy that the plant operators wrote a letter outlining the benefits. Overall, they experienced improvements in worker safety, time savings, productivity, and asset protection, resulting in an overall cost reduction of $212,000 annually.
The automated dispensing saved 45 minutes per day compared to previous manual dispensing processes, resulting in an additional 1 hour of production.
Consistent dosing of smaller concentration ranges enabled lower chemical usage rates, allowing the whey processor to reduce the use of Ultrasil™ 110 from 19 gallons to 11 gallons per day.
Accurate dispensing extending membrane life due to closer pH ranges and the reduction in out-of-range periods from over-dosing during the initial manual chemical addition.
The plant also experienced zero safety related events after installation of the Precision Dispensing System for Membranes, down from an average of 3 incidents per year prior to installation.
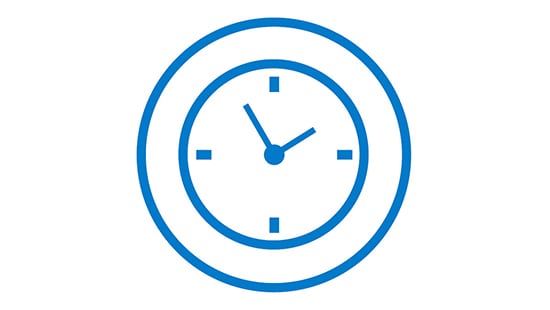
PRODUCTIVITY
$100,000
in additional production

ASSETS
$50,000+
of annual chemical savings

ASSETS
$50,000
in potential membrane life extension

HUMAN HEALTH AND SAFETY
$10,000
in improved worker safety
Total Value Delivered
$212,000 ANNUALLY